SINGAPORE — Bolstered by growing consumer demand and supportive government policies, the indoor agriculture industry is poised to grow strongly across Asia in coming years. And companies from around the world are positioning themselves to sell much-needed technology to these Asian growers.
New data released at the Indoor Ag-Con conference held here last month shows the industry will expand this year across the region, and particularly in places like China and Japan, where food safety is of growing concern. Labor and energy remain two of the industry’s biggest costs and thus among its biggest challenges. That’s why much of the growth in controlled-environment agriculture, or CEA, is underpinned by improvements in LED lighting and in automation.
Indeed, advances in technology are “changing the economics of the [indoor agriculture] industry, and enabling new business models, at a rapid clip,” says a new white paper released at the conference by Newbean Capital, the U.S.-based investment adviser that organized the conference in Singapore, as well as similar events every year in the U.S.
Nearly 1000 greenhouses and plant factories
Asia is home to at least 500 hydroponic greenhouses, Newbean estimates, using data from Cuesta Roble Consulting. The region also has an estimated 450 “plant factories,” with another 75 expected to start operating by the end of this year, Newbean says.
A hydroponic greenhouse, as Newbean defines it, grows crops in a single layer with a nutrient-rich solution replacing soil as the growing medium. Natural sunlight is used through the greenhouse’s transparent roof, usually augmented with artificial lighting. A plant factory, often called a PFAL, for “plant factory with artificial lighting,” grows crops vertically and uses artificial lighting almost exclusively. It may use hydroponic, aeroponic or aquaponic growing methods.
Japan is home to the most plant factories, about 40% of the Asian total, while China and Taiwan have about 25% each, the report says. Both Japan and Taiwan are seeing strong growth: Taiwan had 112 PFALs last year and will have 140 by the end of this year, according to Newbean estimates, while Japan will see its plant factories grow from 185 last year to 210 at the end of 2016.
Those two countries, in fact, have seen 70% annual growth in their indoor agricultural industries since 2009. Yet the markets are far from mature. “There is still plenty of scope for industry development as the industry is small in comparison to the overall vegetable market,” the report says. “Even in Japan, the industry provides less than 0.6% of total vegetable production, and only 18% of consumers are aware of plant factories and have purchased vegetables from them.”
What’s behind the growth
Multiple factors are driving those growth numbers. A major one is changing consumer expectations and behavior when it comes to food consumption, Newbean says. That’s coming from consumer demands for “clean food” — food that’s free of pesticides and comes from reputable sources.
Those demands are understandable. China has faced numerous food scandals in recent years, including melamine in baby food and tainted meat served at some fast food restaurants. Consumers also worry about the source of their food, due to smog in Beijing and other urban centers and the meltdown at Japan’s Fukushima Daiichi nuclear power plant.
Indoor agriculture across Asia has also benefited from supportive government policies, ranging “from subsidies to national policy initiatives,” Newbean says.
China, for example, has declared its support for controlled environment agriculture in its five year plans, and the country has many indoor farming research projects underway. One is the National High Science and Technology Project that brings together 15 universities and companies, with support from the Ministry of Science and Technology, to look for ways to improve plant factory production technology.
And in 2009, the Japanese government launched a project of about 15 billion yen project ($125 million) offering 50 percent subsidies for commercial plant factory construction, as well as subsidies for research, training and other functions. It’s apparently been a success, as about 20 percent of all Japanese plant factory start-ups have received a loan, while 35 percent received both a loan and a subsidy, according to the Newbean report.
Japan’s Plant Factory to Rely on Automation
One of Japan’s biggest indoor growers is Spread, which supplies lettuce to about 2,000 supermarkets across the country. Global marketing manager J.J. Price said at the conference that Spread will start construction this spring on its latest facility, called simply The Vegetable Factory. It will be a 4,800 square meter (52,000 square foot) facility in southern Kyoto, and is slated to start production in mid-2017, Price said.
Among its features will be “high-efficiency water recycling and LEDs that we produce in-house, and it will be highly automated,” he said. “These three innovations address some of the big problems that he industry is facing now.”
Using LEDs will cut the factory’s energy bill by a third, and the process will require only about 110 milliliters of water per head of lettuce. The company’s current operations use eight times as much water per head.
And automation will cut down on labor costs dramatically. While seeding will still be done by hand, most of the rest of the operations —things like transplanting, watering, trimming, controlling lighting and temperatures, and harvesting — will be automated. “Those are the most labor intensive areas, so we’ll focus on those areas,” Price said. The new factory will use 25 workers per day, the company estimates; that’s half of what it uses as its smaller existing facility.
That farm, the Kameoka Plant, is now the world’s largest plant factory in terms of production, turning out 21,000 heads of lettuce per day. Kameoka was built in 2007 and finally turned a profit in 2013 “after six years of trial and error,” CEO Shinji Inada says in a statement.
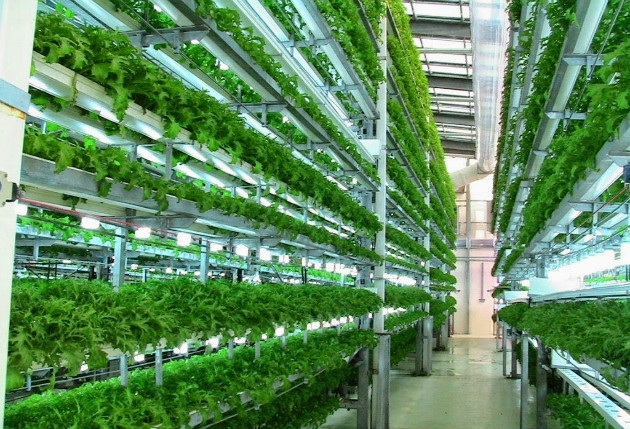
The Kameoka Plant
The Vegetable Factory will have even greater growing capacity. “It will produce 30,000 heads per day, in a smaller building,” Price said. “So the efficiency is going up quite a bit.”
The company is investing up to 2 billion yen — roughly $17 million — in the new facility. Plans call for about 1 billion yen worth of sales each year once it’s fully running, Price said.
Business opportunities for technology providers worldwide
Spread is far from the only grower looking to slash labor costs. Indeed, Price said he’s seeing many other plant factories — especially in the Netherlands — looking to add more automation to their operations as well.
Newbean Capital has noticed the same. Among technology investments, “Lighting, automation and control systems are likely to be the largest areas of technical upgrades,” the report says.
Technology companies are of course very happy to provide those upgrades. While some of the attendees of Newbean’s conference in Singapore are based in Asia, many came from Europe or North America, with some flying 20 hours or more to attend. Several said that in addition to the conference, they had arranged sales calls or other meetings with potential clients across Southeast Asia.
Companies with representatives in attendance at the conference included Philips, Sky Greens, BioGill, Illumitex, Alesca Life Technologies, Bluelab, Heliospectra, Bright Agrotech, Autogrow Systems, Priva and Modular Farms.
So what are indoor growers looking for? One of the most crucial technologies for plant factories — and thus a huge potential business opportunity for technology providers — is lighting. Most new projects now use LEDs, whose efficiencies have improved as costs have come down; prices have plummeted in recent years, and continue to fall, dropping 14% from January 2014 to January 2015, Newbean says. Those drops are forecast to continue. Growers today have a wide range of choices in LED lighting, from turn-key packages offered by companies like Philips Lighting and Lumigrow to customized lighting designs from companies such as Hungry Planet Technology in Austin or Singapore’s Nue Tech.
The lighting sector “has seen rapid innovation over the past decade, as both academic and commercial understanding of the way that plant biology and light interact become more sophisticated,” the Newbean report notes. The industry is only at the beginning stages of that understanding, it goes on, “and consequently there are numerous opportunities for commercialization of new approaches and discoveries.” The investment community sees opportunity here already, as investors put $800 million of venture capital funding into the lighting sector between 2008 and 2010, Newbean says.
Air conditioning — controlling a plant factory’s temperature and humidity — is also crucial to any operation, and growers “consistently seek air conditioning systems that integrate well with farm control systems, and are cheaper and more efficient than those currently available,” Newbean says. This is particularly so for smaller farms, which lack the ability to gain efficiency through scale. Similarly, the report says, growers often use technology to augment the CO2 available in their factories, and may be looking for “cheaper methods of supplying and controlling the carbon dioxide” in the facility.
And like Spread, many growers are increasingly interested in reducing labor costs though robotics and automation, which can help reduce labor costs tremendously.
What’s next
Increased use of automation, like Spread is doing with its new plant, will benefit from improvements in Big Data, as computers can help growers fine-tune lighting, water, temperature and other environmental factors. That, as well as continued advances in LEDs and other inputs, are expected to help bring better yields and increased efficiencies to indoor farming.
That will help when it comes to profits, because indoor agriculture remains a tough industry to make money in. That, Newbean notes, is due to factors like “sub-scale operations” and a “focus on commodity crops” such as head lettuce. Citing Japan as one example, the report says that only a quarter of Japanese plant factories turn a profit, and about half of them break even.
The upshot of that is simple: “A major industry focus going forward is likely to be better profitability,” Newbean says. And growers will try to reach those profits by investing in new technologies — buying improved LEDs, implementing more automation into their processes — and by expanding to reach greater scale.
And as Asian indoor farming continues to mature, Newbean expects that countries will look to export their agricultural technologies and expertise around the world. “To date, this expansion has been contained to a limited number of Asian markets, but we anticipate that these companies will eventually look to Europe, Africa and the United States as export destinations,” the report says.
Indeed, improving profits and sharing methods with the world are among Spread’s goals, according to Price. “Not only do we want to increase our productivity and efficiency, we want to do it at a low cost,” he said. “Part of our mission is to create a sustainable society.” And getting to that point will involve exporting Spread’s knowledge and technology. “We don’t want this kind of technology to be only in Japan,” Price said. “We want it to be in Europe, in the U.S. — we want it to be available around the world.”
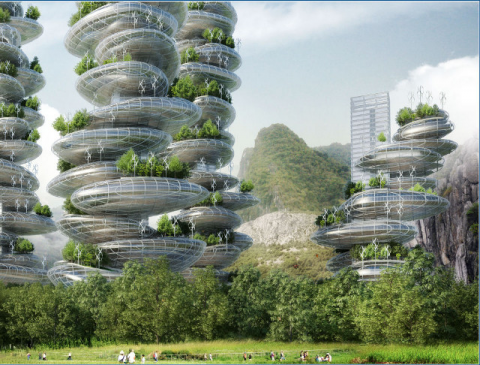
The Chinese city of Shenzhen recently commissioned Vincent Callebaut Architects to come up with an innovative and sustainable building solution for the growing city which includes urban farms.
Cost of operations for some of these indoor facilities has to be astronomical. An alternative is getting into the game on the "local neighborhood" scale. While achieving profits for these growers is also difficult, their person-to-person marketing approach ensures smart growth instead of losing their shirts investing in a large farm.